Cycle Time vs Lead Time: Understanding the Differences
In the world of project management, two terms that often come up are cycle time and lead time. While they may sound similar, they have distinct meanings and play different roles in the production process. Understanding the differences between them is crucial for optimizing workflow efficiency and ensuring customer satisfaction. In this article, we will define these key terms and explore their importance, differences, calculation methods, strategies for reduction, common misconceptions, and how to make the most of them in your operations.
Defining Key Terms: Cycle Time and Lead Time
To begin, let's clarify what exactly cycle time and lead time refer to.
Understanding these two concepts is crucial for businesses aiming to optimize their operations and enhance customer satisfaction.
What is Cycle Time?
Cycle time is the total duration it takes to complete a single unit of work or process, from start to finish. It plays a significant role in assessing the efficiency of a process and identifying potential bottlenecks that may hinder productivity. By analyzing cycle time, organizations can streamline their workflows, improve resource allocation, and ultimately enhance overall productivity.
What is Lead Time?
On the other hand, lead time refers to the total time it takes to fulfill a customer's request, from the moment they make an order to the moment they receive the desired product or service. This encompasses various stages, including order processing, production, quality checks, packaging, shipping, and delivery. By effectively managing lead time, businesses can meet customer expectations, build trust, and gain a competitive edge in the market.
It's important to note that both cycle time and lead time are interconnected and impact the overall efficiency and effectiveness of a business's operations. By monitoring and optimizing these key metrics, organizations can achieve operational excellence and deliver exceptional value to their customers.
The Importance of Cycle Time and Lead Time in Project Management
Now that we have a clear understanding of cycle time and lead time, let's delve into why they are essential in project management.
When it comes to project management, cycle time and lead time are not just technical terms but crucial metrics that can make or break a project's success. Let's explore these concepts further to understand their significance in the realm of project delivery.
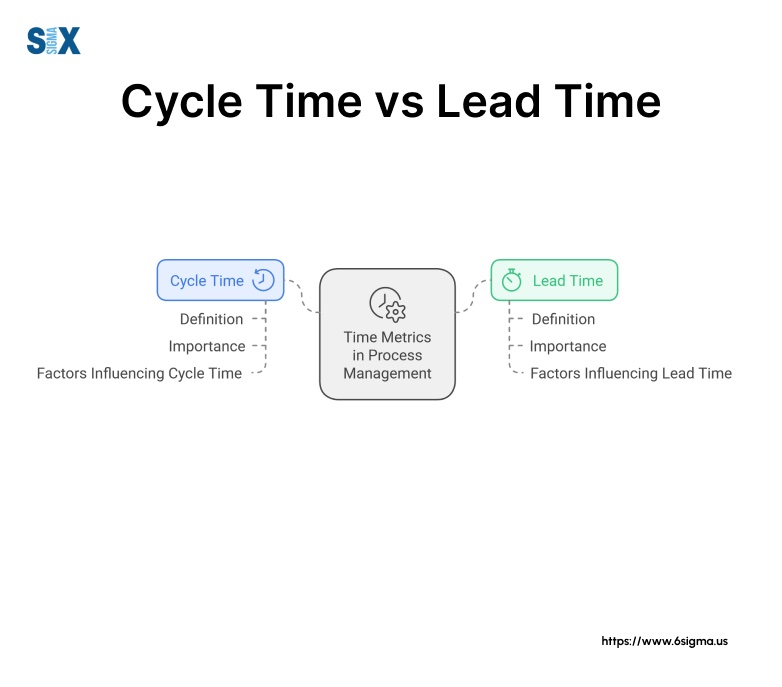
Role of Cycle Time in Efficiency
Cycle time directly impacts efficiency and productivity. By reducing cycle time, organizations can achieve faster turnaround times, improve resource utilization, and increase overall production capacity. Identifying bottlenecks and finding ways to streamline processes can help minimize cycle time and enhance operational efficiency.
Moreover, a shorter cycle time can also result in quicker feedback loops, allowing teams to iterate and improve their work rapidly. This iterative process not only boosts efficiency but also fosters a culture of continuous improvement within the project team.
Role of Lead Time in Customer Satisfaction
Lead time plays a crucial role in ensuring customer satisfaction. Shorter lead times lead to faster delivery, which is often a key factor for customers when choosing between different suppliers. Meeting or exceeding customer expectations in terms of delivery time can significantly enhance customer loyalty and satisfaction.
Additionally, a shorter lead time can give organizations a competitive edge in the market by enabling them to respond swiftly to changing customer demands. This agility in delivery can help businesses stay ahead of the competition and build a reputation for reliability and responsiveness.
Differences Between Cycle Time and Lead Time
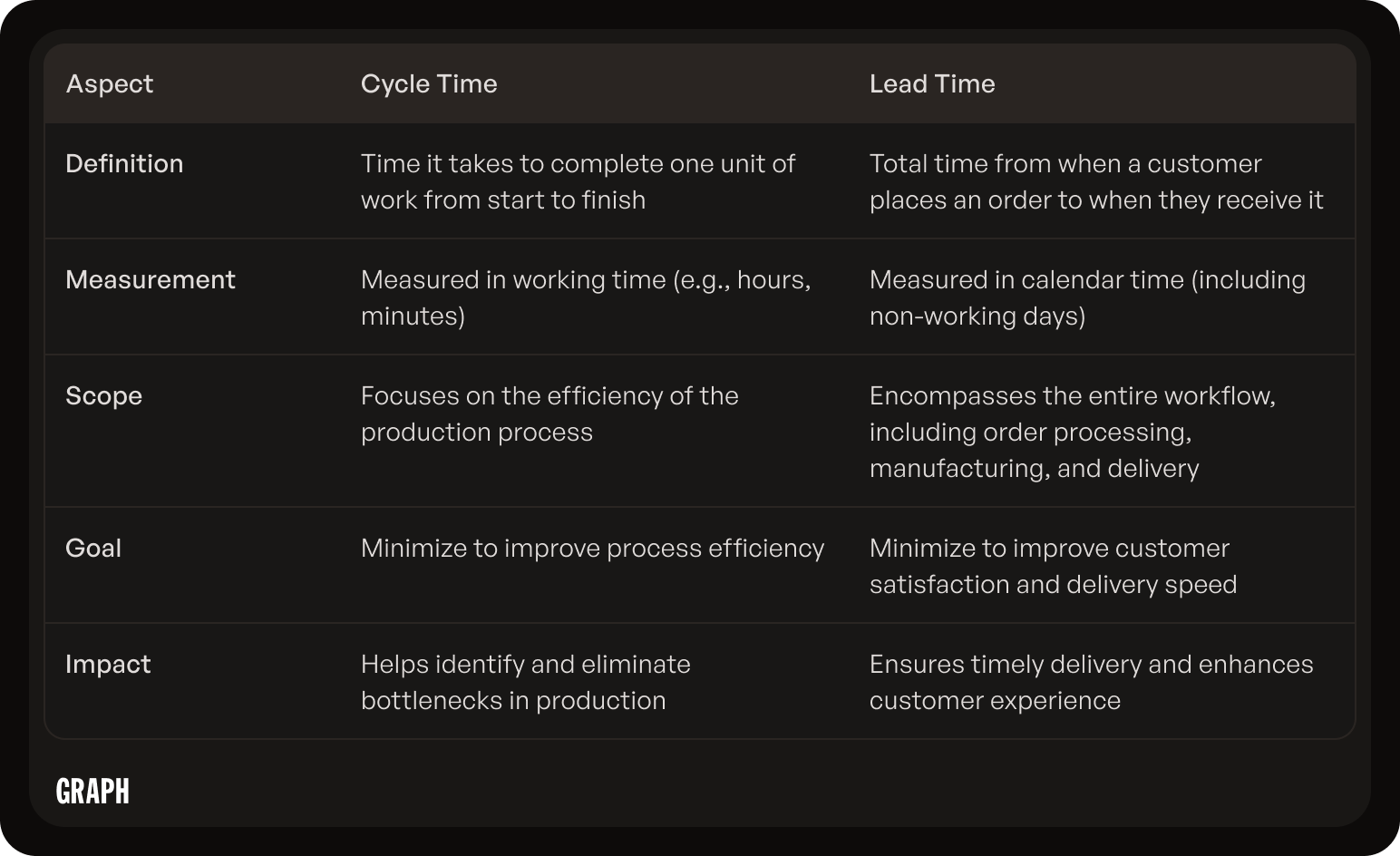
Although cycle time and lead time both refer to time durations, there are distinct differences between them that are important to understand.
When it comes to manufacturing processes, the concept of cycle time is crucial. It represents the total time taken to complete one cycle of an operation or task. This includes all the individual steps involved in the process, from start to finish. By analyzing and optimizing cycle time, businesses can identify bottlenecks and streamline their production processes to improve efficiency and productivity.
Measurement Parameters
One key difference lies in the parameters used to measure cycle time and lead time. Cycle time is typically measured using units of time, while lead time is measured in calendar days, which includes non-working days.
Lead time, on the other hand, encompasses a broader scope. It not only considers the time taken to complete a task but also includes the time between the initiation of a process and its ultimate completion. This includes factors such as order processing, material sourcing, and transportation. By understanding lead time, businesses can better manage customer expectations and ensure timely delivery of products or services.
Impact on Production Process
Cycle time focuses on the efficiency of the production process itself, aiming to minimize the time required for each individual operation. Lead time, on the other hand, takes into account the entire workflow, including processing, manufacturing, and distribution, to ensure timely delivery to the end customer.
Moreover, lead time plays a crucial role in inventory management and supply chain optimization. By accurately estimating lead times for different processes, businesses can reduce excess inventory, minimize stockouts, and improve overall operational efficiency. This strategic approach not only enhances customer satisfaction but also helps businesses save costs and stay competitive in the market.
How to Calculate Cycle Time and Lead Time
Knowing how to calculate cycle time and lead time accurately is essential for monitoring and optimizing these metrics. Let's break down the steps for each calculation.
Understanding cycle time and lead time is crucial for businesses looking to improve their operational efficiency and customer satisfaction. By accurately calculating these metrics, organizations can identify bottlenecks, streamline processes, and deliver products and services more effectively.
Steps to Calculate Cycle Time
To calculate cycle time, start by determining the total time it takes to complete a particular process or operation. This can involve a single task or a series of interconnected tasks. Divide this total time by the number of units produced or processed within that period.
Cycle time is a key performance indicator that helps organizations assess their production speed and efficiency. By analyzing cycle time data, businesses can pinpoint areas for improvement, implement changes to optimize workflows, and ultimately enhance productivity.
Steps to Calculate Lead Time
Calculating lead time involves tracking the time it takes for a customer's request to be fulfilled from the moment they place an order to the moment they receive the final product or service. This includes the time required for processing, production, transportation, and delivery. Keep in mind that lead time may vary depending on the specific product or service being provided.
Lead time is a critical metric for businesses aiming to meet customer expectations and maintain a competitive edge. By accurately calculating lead time, organizations can streamline their supply chain, improve order fulfillment processes, and enhance overall customer satisfaction.
Strategies for Reducing Cycle Time and Lead Time
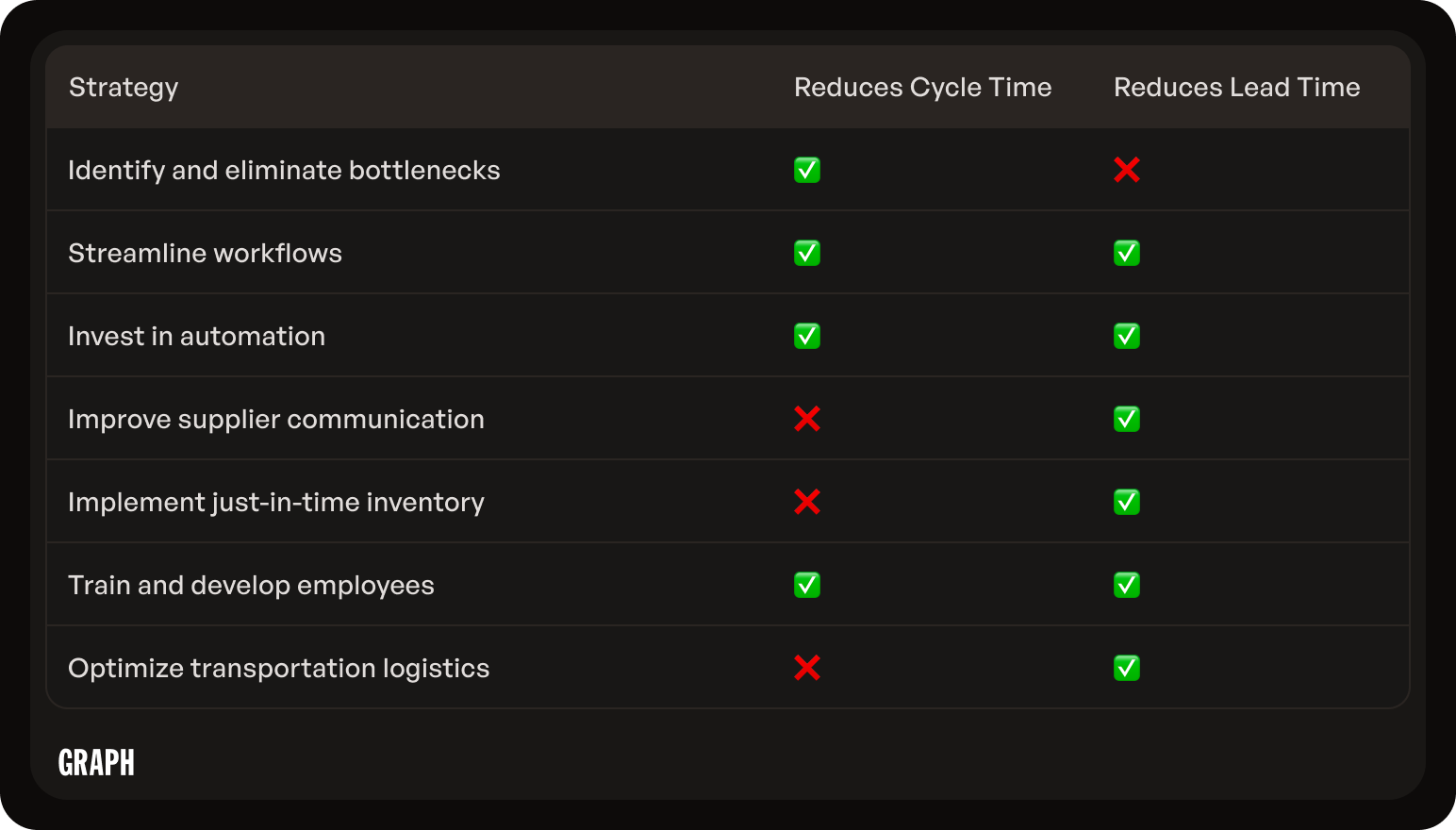
Reducing cycle time and lead time can significantly benefit your operations in terms of efficiency and customer satisfaction. Let's explore some effective strategies for achieving this.
Efficiently managing cycle time and lead time is crucial for businesses looking to stay competitive in today's fast-paced market. By streamlining these processes, companies can not only improve productivity but also enhance their ability to respond quickly to customer demands and market changes.
Techniques for Shortening Cycle Time
One way to shorten cycle time is by identifying any bottlenecks or inefficiencies in the production process and implementing improvements. Applying lean manufacturing principles, adopting automation technologies, reorganizing workflows, and optimizing supply chain logistics are just a few approaches that can help reduce cycle time.
Furthermore, investing in employee training and development can also play a significant role in reducing cycle time. Well-trained staff are more efficient in their tasks, leading to smoother operations and faster turnaround times.
Methods for Minimizing Lead Time
Minimizing lead time requires a holistic approach that focuses on improving various stages of the production and delivery process. Strategies may include reducing processing and manufacturing time, enhancing transportation and logistics efficiency, and implementing just-in-time inventory management systems to minimize delays.
Collaborating closely with suppliers and partners is another effective way to minimize lead time. By establishing strong relationships and clear communication channels, businesses can ensure timely delivery of materials and components, ultimately speeding up the overall production process.
Misconceptions About Cycle Time and Lead Time
Despite their importance, cycle time and lead time can be surrounded by various misconceptions or myths. Let's debunk some of the most common ones.
When it comes to cycle time, there is a misconception that shorter cycle times always equate to better performance. While it is true that reducing cycle time can enhance efficiency, it is essential to strike a balance between speed and quality. Overemphasizing speed without considering the impact on other aspects of the process can lead to subpar results. It is crucial to focus on optimizing the entire workflow rather than just speeding up individual tasks.
Common Myths About Cycle Time
One common myth is that minimizing cycle time always leads to improved productivity. While reducing cycle time can increase efficiency, it is crucial to consider the impact on quality and overall process optimization. Simply focusing on speed without considering other factors can result in compromised outcomes.
Moreover, another misconception about cycle time is that it is a fixed metric that cannot be altered. In reality, cycle time is a dynamic measure that can be influenced by process improvements, resource allocation, and workflow adjustments. By continuously analyzing and optimizing cycle times, organizations can adapt to changing demands and enhance their operational effectiveness.
Common Myths About Lead Time
Another common myth is that lead time is solely determined by manufacturing processes. In reality, lead time is influenced by various factors, including order processing, procurement, transportation, and other logistics. Understanding the entire workflow is essential for effectively managing and reducing lead time.
Furthermore, there is a misconception that lead time is a standalone metric that does not impact other areas of the business. In truth, lead time plays a critical role in customer satisfaction, inventory management, and overall operational efficiency. By streamlining processes across departments and suppliers, organizations can reduce lead times and improve their competitive edge in the market.
Conclusion: Making the Most of Cycle Time and Lead Time in Your Operations
In conclusion, cycle time and lead time are vital metrics in project management, offering valuable insights into efficiency, operational performance, and customer satisfaction. By understanding their differences, accurately calculating them, implementing effective strategies for reduction, and dispelling common misconceptions, you can optimize your operations and deliver exceptional results to your customers. Embrace these metrics as valuable tools that can drive continuous improvement and success in your organization.