MTBF vs MTTF: Understanding the Key Differences
In the world of system reliability, metrics such as MTBF (Mean Time Between Failures) and MTTF (Mean Time to Failure) play a crucial role. These metrics help engineers assess and predict the reliability of various systems and components. While MTBF and MTTF may seem similar, there are key differences between the two that must be understood. This article aims to shed light on these differences, explain the importance of MTBF and MTTF in system reliability, debunk common misconceptions, and provide guidance on interpreting the data. Additionally, the article will explore how MTBF and MTTF factor into maintenance planning and their relationship with other reliability metrics.
Defining MTBF and MTTF
What is MTBF?
MTBF, or Mean Time Between Failures, is a reliability metric that quantifies the expected average time between two consecutive failures of a system or component under normal operation. It is typically calculated by dividing the total operating time by the number of failures encountered during that period.
MTBF helps engineers evaluate the reliability of a system by providing an estimate of the average time it can operate without experiencing a failure. It allows for comparisons between different systems and components, helping in the selection of more reliable options.
When considering the design and implementation of complex systems such as aircraft engines, data centers, or medical devices, MTBF plays a crucial role in predicting maintenance schedules and optimizing system performance. By understanding the MTBF of critical components, engineers can proactively address potential issues and minimize downtime, ultimately improving overall system reliability.
What is MTTF?
MTTF, or Mean Time to Failure, is a reliability metric that represents the average time a system or component is expected to operate before its first failure. Unlike MTBF, MTTF does not consider repair or maintenance time.
MTTF is often used when studying products with a limited life span or systems where repair is not feasible or practical. It is commonly used to analyze the reliability of consumer electronics, electronic components, and other similar devices.
When manufacturers are designing products with predetermined life expectancies, understanding the MTTF becomes crucial in ensuring customer satisfaction and product performance. By conducting thorough reliability tests and simulations based on MTTF data, companies can make informed decisions about product warranties, replacement policies, and overall quality assurance measures.
The Importance of MTBF and MTTF in System Reliability
MTBF (Mean Time Between Failures) and MTTF (Mean Time To Failure) are crucial indicators for system reliability analysis, helping engineers predict and improve the performance of various systems. By understanding these metrics, engineers can:
- Evaluate the reliability of different systems and components, aiding in the selection of more robust and dependable options.
- Identify potential weak points in a system and focus on improving their reliability, thus enhancing overall system performance.
- Estimate maintenance requirements, allowing organizations to plan and optimize maintenance activities more effectively.
- Assess system availability and downtime, aiding in the identification of potential bottlenecks and areas for improvement.
To accomplish these objectives, it is essential to comprehend the key differences between MTBF and MTTF, as well as their respective calculation methods and applications in various systems.
MTBF is commonly used for systems that can be repaired and returned to service after a failure, such as servers or manufacturing equipment. It is calculated by dividing the total operational time by the number of failures that occur within that time period. On the other hand, MTTF is often used for systems that are replaced rather than repaired, like light bulbs or fuses. MTTF represents the average time until a non-repairable system fails.
Understanding the nuances of MTBF and MTTF is crucial for engineers to make informed decisions about system design, maintenance schedules, and overall reliability. By utilizing these metrics effectively, organizations can minimize downtime, reduce maintenance costs, and improve customer satisfaction through more reliable products and services.
Key Differences between MTBF and MTTF
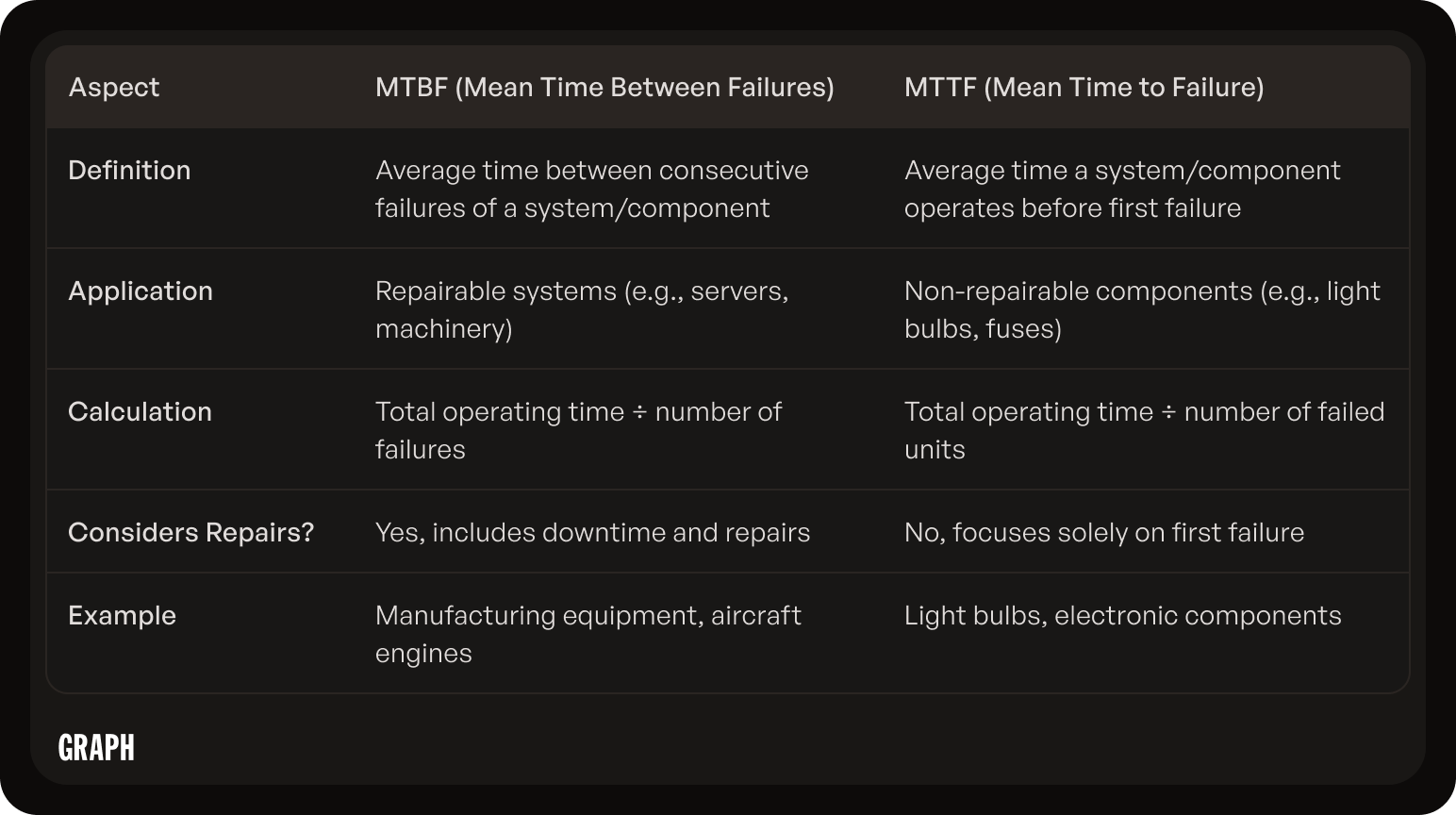
Calculation Method
The calculation of MTBF involves dividing the total operating time by the number of failures. This method takes into account both the operational uptime and downtime due to failures. On the other hand, MTTF is calculated by dividing the total operating time by the number of units that failed.
It is important to note that MTBF assumes the occurrence of repair or maintenance actions to bring a failed system or component back to an operational state. In contrast, MTTF does not consider repair time, as it focuses solely on the first failure of the system or component.
When calculating MTBF, it is crucial to consider the Mean Time To Repair (MTTR), which represents the average time taken to repair a failed system or component. This metric plays a significant role in determining the overall system reliability and availability.
Application in Different Systems
MTBF is commonly used in systems that are repairable, where the downtime resulting from failures can be reduced by repair or replacement actions. It is particularly relevant in industries such as manufacturing, telecommunications, and power generation. In manufacturing plants, for example, knowing the MTBF of critical machinery helps in scheduling preventive maintenance tasks to minimize unplanned downtime.
On the other hand, MTTF is more appropriate for non-repairable or consumable components, where failure is typically an irreversible event. Industries such as consumer electronics, automotive, and medical devices frequently utilize MTTF in their reliability assessments. For instance, in the automotive sector, the MTTF of safety-critical components like airbags is a crucial factor in ensuring passenger safety and compliance with industry regulations.
Misconceptions about MTBF and MTTF
There are several common misconceptions surrounding MTBF and MTTF that can lead to misinterpretation of reliability data. One such misconception is considering MTBF as a direct measure of the system's working life. MTBF only provides an estimation of the average time between failures; it does not indicate how long a system will operate before reaching the end of its lifecycle.
Another misconception is assuming that a higher MTBF value automatically signifies a more reliable system. While a higher MTBF suggests a longer average time between failures, it does not guarantee the absence of critical failures or the overall quality and performance of the system.
Understanding these misconceptions is crucial for accurately interpreting reliability data and making informed decisions based on the MTBF and MTTF values.
It is important to note that MTBF and MTTF are essential metrics in the field of reliability engineering. MTBF is commonly used in industries such as manufacturing, aerospace, and telecommunications to assess the reliability of systems and components. It helps organizations predict maintenance schedules, plan for downtime, and improve overall system performance.
On the other hand, MTTF is often utilized in industries where repair or replacement is the preferred maintenance strategy. It provides valuable insights into the expected lifespan of a component or system under normal operating conditions. By understanding the differences between MTBF and MTTF, engineers and decision-makers can better evaluate the reliability and durability of their products.
How to Interpret MTBF and MTTF Data
Understanding MTBF Data
MTBF data can be interpreted in various ways depending on the system or component being analyzed. If the objective is to compare different options, selecting the one with the highest MTBF value may provide a higher probability of longer operational periods without failures.
However, it is essential to consider the nature of the failures. A high MTBF achieved by mitigating minor and non-critical failures may not be as valuable as a lower MTBF that primarily addresses severe impact failures.
Furthermore, MTBF should not be the sole metric considered in decision-making processes. Other reliability metrics, such as failure rate and maintenance costs, should also be evaluated to obtain a comprehensive understanding of system reliability.
When analyzing MTBF data, it is crucial to delve deeper into the failure modes and effects analysis (FMEA) to identify the potential risks associated with each failure mode. By understanding the criticality of different failure modes, organizations can prioritize their maintenance strategies and resources effectively.
Understanding MTTF Data
MTTF data provides insights into the expected time until the first failure occurs. For non-repairable components, a higher MTTF value indicates a longer expected lifespan before failure, making it a desirable characteristic.
When comparing different components or systems, MTTF can influence the decision-making process. However, factors such as performance requirements, availability of backup options, and cost should also be considered alongside the MTTF value.
It is important to recognize that MTTF is based on the assumption of constant failure rates over time, which may not always hold true in practical scenarios. Variations in operating conditions, environmental factors, and maintenance practices can impact the actual reliability of a component or system beyond what MTTF values suggest.
The Role of MTBF and MTTF in Maintenance Planning
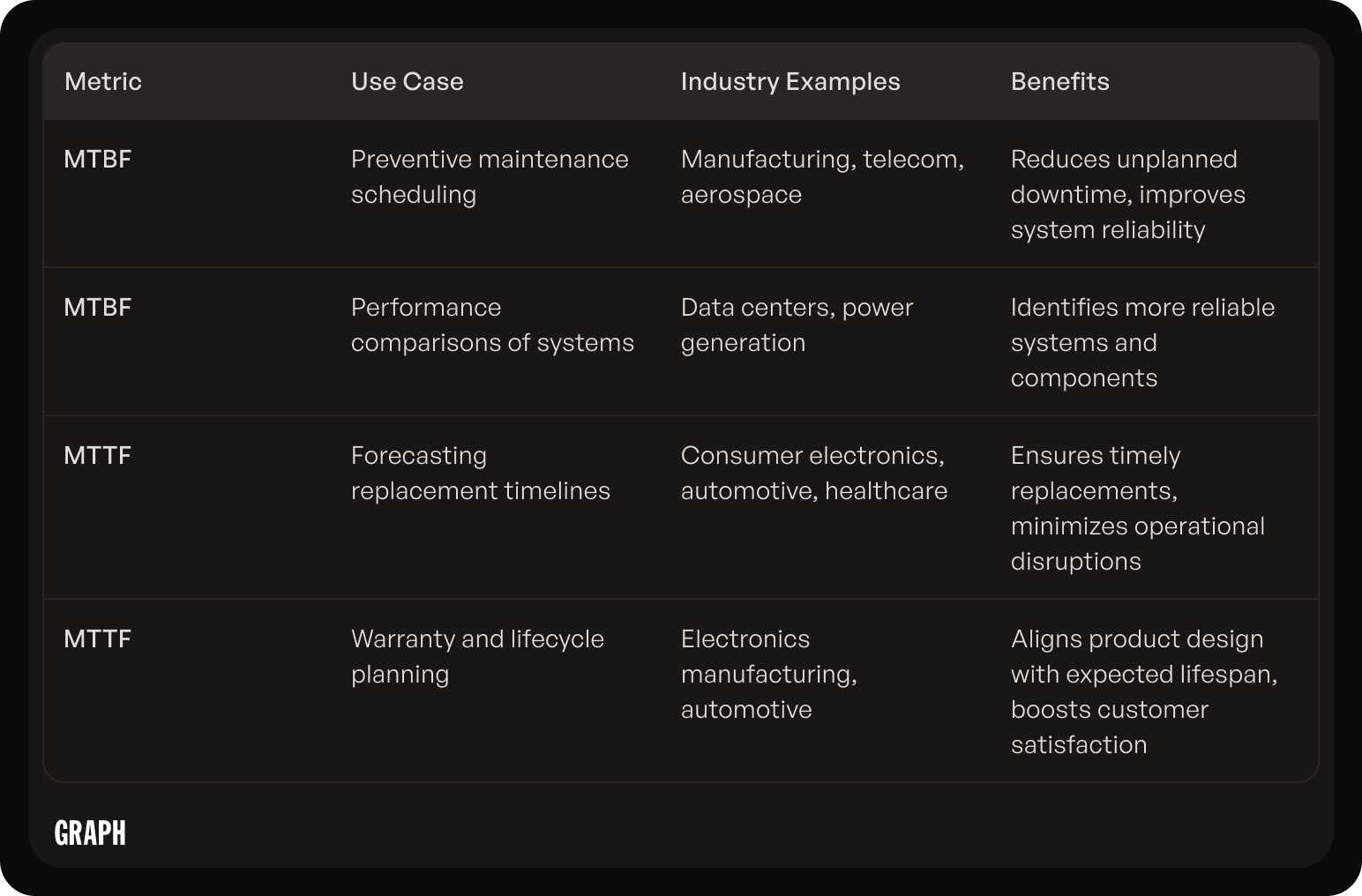
MTBF (Mean Time Between Failures) and MTTF (Mean Time To Failure) are key metrics in maintenance planning, offering valuable insights into the reliability and failure patterns of systems and components. These metrics are essential for organizations looking to enhance operational efficiency and minimize disruptions due to unexpected breakdowns.
When it comes to repairable systems, MTBF serves as a critical parameter for establishing preventive maintenance schedules. By calculating the average time between failures, maintenance teams can proactively schedule maintenance activities to address potential issues before they escalate. This proactive approach not only reduces the likelihood of unexpected failures but also helps in optimizing maintenance resources and improving overall system reliability.
On the other hand, MTTF is particularly relevant for non-repairable systems where components are replaced rather than repaired. Understanding the mean time to failure allows organizations to forecast the expected lifespan of these components, enabling timely replacements and upgrades to prevent costly downtime and operational disruptions.
By integrating MTBF and MTTF data into maintenance planning processes, organizations can make informed decisions that lead to more efficient resource allocation, reduced maintenance costs, and increased system availability. These metrics serve as valuable tools for maintenance managers and engineers seeking to strike a balance between operational performance and maintenance expenditures.
MTBF and MTTF in the Context of Other Reliability Metrics
MTBF, MTTF, and Failure Rate
Failure rate, often denoted as λ, is another critical reliability metric. It represents the probability of failure per unit of time. MTBF can be calculated as the reciprocal of the failure rate (MTBF = 1/λ). Failure rate provides insights into the failure behavior of a system, aiding in the estimation of failures over time.
Understanding failure rates is essential for predicting maintenance needs and optimizing system performance. By monitoring and analyzing failure rates, organizations can implement proactive maintenance strategies to prevent costly downtime and ensure operational efficiency.
In comparison, MTTF measures the expected time to the first failure, complementing the failure rate by providing a lifespan estimation. Together, these metrics provide a comprehensive understanding of the reliability characteristics of a system or component.
MTBF, MTTF, and Life Expectancy
Life expectancy refers to the anticipated lifespan of a system or component until it becomes obsolete or reaches the end of its intended use. While MTBF and MTTF are important factors in assessing reliability, they do not directly reflect the overall life expectancy of a system or component.
Life expectancy considers not only failures but also factors such as technological advancements, changes in user requirements, and obsolescence of components. Understanding the interplay between MTBF, MTTF, and life expectancy is crucial for comprehensive reliability and lifecycle assessments.
Moreover, life expectancy plays a vital role in strategic planning and decision-making processes. Organizations must consider the projected life expectancy of systems and components when developing long-term maintenance schedules, budgeting for replacements, and aligning technology investments with business goals.
Conclusion: Choosing Between MTBF and MTTF
When evaluating system reliability, it is essential to consider both MTBF and MTTF metrics, along with other relevant reliability parameters. While MTBF focuses on the time between failures for repairable systems, MTTF provides insights into the lifespan before the first failure for non-repairable or consumable components.
By understanding the key differences between MTBF and MTTF, engineers can make informed decisions regarding system selection, maintenance planning, and reliability improvements. It is important to remember that while these metrics provide valuable insights, they should not be the sole basis for decision-making. Holistic assessments, considering factors such as failure rate, life expectancy, and cost, are essential for ensuring reliable and robust systems.