Quality Assurance vs Quality Engineering: Understanding the Key Differences
Quality Assurance (QA) and Quality Engineering (QE) are two crucial aspects of the product development and manufacturing process. While they may sound similar, they have distinct roles and responsibilities. In this article, we will explore the key differences between QA and QE, their impact on businesses, and factors to consider when choosing between them.
Defining Quality Assurance
Quality Assurance is a systematic approach to ensure that a product or service meets the specified requirements and customer expectations. It focuses on preventing defects and improving the overall quality of the deliverables.
Quality Assurance goes beyond just checking for bugs or errors; it encompasses a comprehensive process that involves meticulous planning, execution, and monitoring to guarantee that the final product meets the highest standards of quality. By implementing rigorous quality assurance measures, organizations can enhance customer satisfaction, build trust, and establish a reputation for delivering excellence.
The Role of Quality Assurance in Product Development
QA plays a critical role in the software development lifecycle. It involves activities such as requirement analysis, test planning, test execution, defect tracking, and release management. The goal is to identify and rectify issues early in the development process to minimize risks and ensure a high-quality end product.
Quality Assurance professionals work closely with cross-functional teams to establish quality standards, define testing criteria, and execute test cases to validate the functionality and performance of the product. By collaborating with developers, designers, and stakeholders, QA specialists contribute to the seamless delivery of products that meet or exceed customer expectations.
Key Principles of Quality Assurance
QA is guided by several key principles:
- Prevention: QA focuses on preventing defects rather than just identifying and fixing them.
- Process Improvement: QA continuously seeks to improve processes to enhance efficiency and quality.
- Risk Management: QA identifies and mitigates risks that may affect the product's quality and reliability.
- Customer Focus: QA ensures that the customer's needs and expectations are met or exceeded.
Embracing these principles allows organizations to instill a culture of quality throughout their operations, driving continuous improvement and innovation. Quality Assurance serves as a cornerstone for building robust products, fostering customer loyalty, and achieving sustainable growth in today's competitive market landscape.
Understanding Quality Engineering
Quality Engineering, on the other hand, is a holistic approach that focuses on achieving the desired level of quality throughout the manufacturing process. It aims to optimize production systems, reduce variability, and improve overall product quality.
Quality Engineering is not just about meeting quality standards; it is about exceeding them. By implementing rigorous processes and quality control measures, companies can ensure that their products not only meet but surpass customer expectations, leading to increased customer satisfaction and loyalty.
The Function of Quality Engineering in Manufacturing
Quality Engineering plays a crucial role in manufacturing industries. It involves activities such as process optimization, statistical analysis, failure analysis, and continuous improvement. The goal is to ensure that products meet the required quality standards, comply with regulations, and exceed customer expectations.
One key aspect of Quality Engineering is risk management. By identifying potential risks in the manufacturing process early on, Quality Engineers can develop strategies to mitigate these risks and prevent quality issues from arising. This proactive approach helps companies avoid costly recalls and reputation damage.
Core Concepts of Quality Engineering
Quality Engineering follows several core concepts:
- Process Capability: QE assesses the capability of a manufacturing process to consistently meet the desired specifications.
- Statistical Analysis: QE utilizes statistical tools to analyze data and identify trends, patterns, and potential quality issues.
- Root Cause Analysis: QE investigates the underlying causes of quality problems and implements corrective actions.
- Continuous Improvement: QE focuses on ongoing process improvement to drive efficiency and enhance product quality.
Furthermore, Quality Engineering emphasizes the importance of collaboration across departments. By fostering communication and cooperation between engineering, production, and quality assurance teams, companies can streamline processes, identify issues early, and work together to implement effective solutions. This cross-functional approach not only improves product quality but also promotes a culture of continuous learning and innovation within the organization.
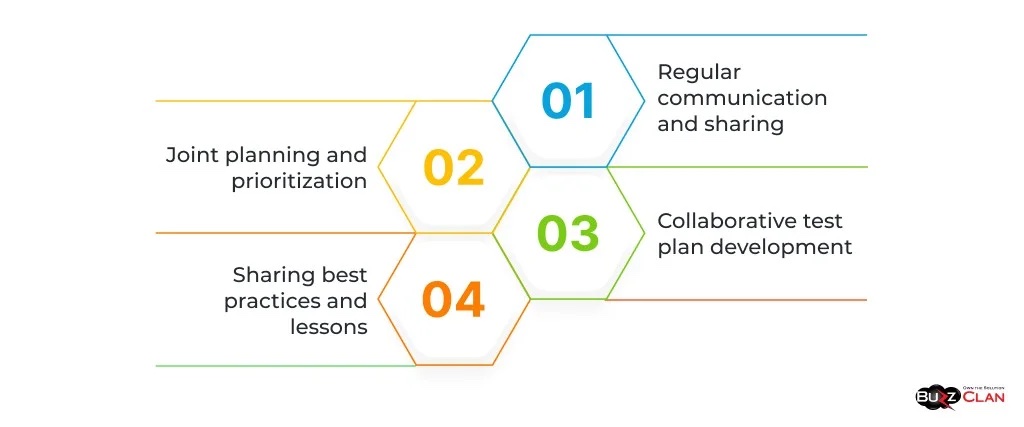
Comparing Quality Assurance and Quality Engineering
While QA and QE share some similarities, they have distinct roles and responsibilities within an organization.
Quality Assurance (QA) and Quality Engineering (QE) are both crucial components of ensuring product quality and customer satisfaction in various industries. QA focuses on the software development process, ensuring that the final product meets specified requirements, while QE is dedicated to optimizing manufacturing processes, reducing variability, and enhancing overall product quality.
Similarities Between Quality Assurance and Quality Engineering
Both QA and QE strive to improve product quality, customer satisfaction, and the overall efficiency of the development or manufacturing process. They both rely on data analysis and risk management techniques to achieve their objectives.
Furthermore, both QA and QE professionals utilize cutting-edge technologies and methodologies to streamline processes and enhance quality standards. Continuous improvement is at the core of their practices, as they aim to identify areas for enhancement and implement solutions to drive excellence.
Distinct Differences in Roles and Responsibilities
The main difference between QA and QE lies in their focus and scope. QA primarily focuses on the software development process and ensuring that the final product meets the specified requirements. On the other hand, QE focuses on optimizing the manufacturing process, reducing variability, and improving overall product quality.
QA professionals typically work closely with software developers, testers, and project managers. They are responsible for developing test plans, executing tests, identifying defects, and ensuring that the software meets the desired quality standards.
On the other hand, QE professionals work closely with manufacturing engineers, process owners, and quality managers. They are responsible for analyzing production data, identifying process bottlenecks, implementing process improvements, and ensuring that products meet the required quality standards.
Both QA and QE play vital roles in driving organizational success and fostering a culture of quality excellence. By collaborating effectively and leveraging their unique skill sets, these professionals contribute to the overall growth and reputation of the company.
The Impact of Quality Assurance and Quality Engineering on Business
Both Quality Assurance (QA) and Quality Engineering (QE) are integral components of a successful business strategy, playing a crucial role in driving business success and enhancing customer satisfaction. These two disciplines work hand in hand to ensure that products and services meet the highest standards of quality and reliability.
How Quality Assurance Enhances Customer Satisfaction
Quality Assurance (QA) is the process of monitoring and improving the quality of products and services offered by a business. It ensures that the final product meets the customer's requirements and expectations by implementing rigorous testing procedures and quality control measures. By preventing defects and identifying issues early in the development process, QA helps deliver high-quality software that is reliable, user-friendly, and bug-free. This meticulous attention to detail not only enhances customer satisfaction but also fosters brand loyalty and trust among consumers.
The Role of Quality Engineering in Reducing Production Costs
Quality Engineering (QE) is a systematic approach to optimizing the manufacturing process to reduce waste, improve efficiency, and minimize defects. By focusing on process improvements and reducing variability, QE plays a crucial role in lowering production costs and increasing profitability for businesses. Through the implementation of advanced quality control techniques and continuous process monitoring, QE ensures that products meet the required quality standards, thereby reducing the risk of costly recalls or customer complaints. By investing in quality engineering practices, businesses can streamline their operations, enhance product quality, and gain a competitive edge in the market.
Choosing Between Quality Assurance and Quality Engineering
When deciding between QA and QE, several factors should be considered, including the nature of the product or service, the industry, and the organization's goals and priorities.
Quality Assurance (QA) and Quality Engineering (QE) are both crucial components in ensuring the quality of products and services. While QA focuses on processes and methodologies to prevent defects and errors in the final product, QE emphasizes the design and implementation of testing frameworks and tools to improve the overall quality of the product. Understanding the distinction between the two disciplines is essential in making an informed decision.
Factors to Consider When Deciding
Some key factors to consider include:
- Product Complexity: If the product is software-based, QA will be more relevant. If it involves complex manufacturing processes, QE will be more appropriate.
- Industry Regulations: Industries with strict quality and regulatory standards may require a stronger emphasis on QA or QE.
- Resource Availability: Consider the availability of skilled professionals and the organization's capacity to invest in QA or QE teams.
Furthermore, it is essential to evaluate the scalability of the chosen quality approach. QA processes can be scaled more easily across different projects and teams, while QE practices may require more specialized skills and resources. Finding the right balance between the two can significantly impact the overall quality of the deliverables.
The Importance of Aligning with Business Goals
Ultimately, the decision should align with the organization's overall business goals and objectives. It may be beneficial to leverage both QA and QE to ensure the highest level of quality throughout the entire product lifecycle. By integrating QA and QE practices seamlessly into the development process, organizations can achieve greater efficiency, reduce time-to-market, and enhance customer satisfaction. Collaboration between QA and QE teams can lead to a more holistic quality strategy that addresses both functional and non-functional aspects of the product, resulting in a superior end-user experience.
The Future of Quality Assurance and Quality Engineering
As technology advances and industries evolve, QA and QE will continue to play a vital role in ensuring product quality and customer satisfaction. With the ever-increasing demands for high-quality software and products, organizations are constantly seeking new ways to improve their QA and QE practices.
Emerging Trends in Quality Assurance
Some emerging trends in QA include:
- Shift Left Testing: Moving testing activities earlier in the development process to detect and fix issues early on. This approach allows for faster feedback and reduces the cost of fixing defects later in the development cycle.
- Automation: Increasing the use of test automation to improve efficiency and reduce manual effort. By automating repetitive and time-consuming tasks, QA teams can focus on more critical aspects of testing, such as exploratory testing and test case design.
- DevOps: Integrating QA practices into the continuous delivery and deployment pipelines for faster and more reliable software releases. By collaborating closely with development and operations teams, QA professionals can ensure that quality is built into every stage of the software development lifecycle.
Innovations in Quality Engineering
Quality Engineering is also experiencing advancements to meet the evolving needs of modern manufacturing processes. Some innovations include:
- Advanced Analytics: Leveraging machine learning and artificial intelligence to analyze production data and identify patterns. By harnessing the power of data, organizations can gain valuable insights into their manufacturing processes, enabling them to make data-driven decisions and optimize quality.
- Internet of Things (IoT): Integrating IoT devices to monitor and control manufacturing processes in real-time. With IoT devices, organizations can collect real-time data on various parameters, such as temperature, pressure, and humidity, allowing them to proactively identify and address quality issues.
- Industry 4.0: Embracing smart manufacturing technologies such as robotics, automation, and cyber-physical systems. Industry 4.0 revolutionizes the manufacturing landscape by enabling interconnected systems that communicate and collaborate with each other, resulting in improved efficiency, productivity, and quality.
These innovations in quality engineering not only enhance the efficiency and effectiveness of manufacturing processes but also pave the way for new business models and revenue streams. By embracing these technologies, organizations can stay ahead of the competition and deliver high-quality products that meet customer expectations.
In conclusion, Quality Assurance and Quality Engineering are critical components in ensuring product quality, customer satisfaction, and business success. While QA focuses on the software development process, QE optimizes manufacturing processes. By understanding their differences and aligning with business goals, organizations can make informed decisions to drive quality and efficiency in their products and services.