The Importance of Reliability Engineering in Modern Industries
Reliability engineering plays a crucial role in modern industries, ensuring that products, processes, and systems function consistently and perform optimally. In a world where technology evolves at a rapid pace, it becomes imperative for companies to prioritize reliability in order to meet customer demands and maintain a competitive edge. By understanding the principles of reliability engineering and its intersection with various industries, businesses can reap numerous benefits while navigating the challenges that come with its implementation.
Understanding Reliability Engineering
Reliability engineering encompasses a set of methods, techniques, and strategies aimed at improving the dependability, availability, and performance of products and systems throughout their lifecycle. It involves analyzing, identifying, and mitigating risks to ensure that products consistently meet their intended functionality.
Definition and Key Principles of Reliability Engineering
Reliability engineering is the discipline of designing and testing products, processes, and systems with the ultimate goal of minimizing failures and maximizing performance. It involves employing statistical methods, quality control techniques, and risk analysis tools to measure reliability metrics such as failure rate, mean time between failures (MTBF), and mean time to repair (MTTR).
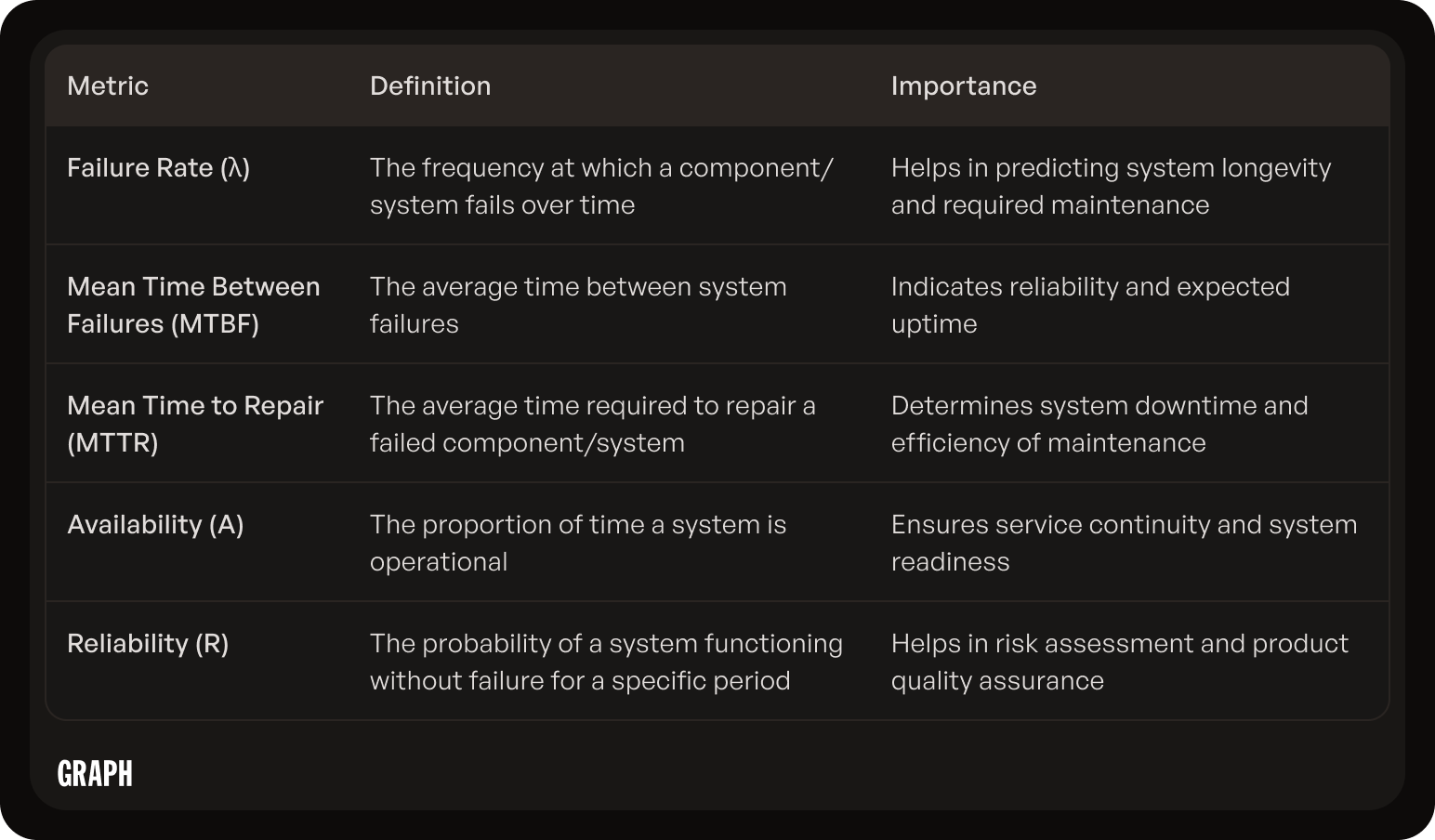
Some key principles of reliability engineering include:
- Understanding customer requirements and translating them into specific reliability objectives
- Applying mathematical modeling and analysis to predict and improve reliability
- Incorporating redundancy and fault-tolerant designs to enhance system reliability
- Implementing proactive maintenance and monitoring strategies to detect and prevent failures
Reliability engineering is a multidisciplinary field that draws upon various areas of expertise. For example, it involves knowledge of materials science to select the most suitable materials for a product's intended use, as well as an understanding of electrical engineering principles to design reliable electronic systems. Additionally, reliability engineers often collaborate with software engineers to ensure the reliability of software-based systems.
The Role of a Reliability Engineer
A reliability engineer is responsible for ensuring that products and systems meet the desired levels of dependability, safety, and performance. Their role involves conducting risk assessments, designing reliability tests, and analyzing failure data to identify potential weaknesses and improve reliability.
Moreover, reliability engineers collaborate closely with design and manufacturing teams to incorporate reliability considerations throughout the product development process. They work with suppliers, customers, and stakeholders to establish reliability requirements, develop test plans, and provide recommendations for product enhancements.
Furthermore, reliability engineers play a crucial role in the field of maintenance. They develop maintenance strategies and schedules to optimize the performance and reliability of products and systems. By implementing predictive maintenance techniques, such as condition monitoring and trend analysis, reliability engineers can identify potential failures before they occur, allowing for timely repairs and minimizing downtime.
In summary, reliability engineering is a vital discipline that ensures the dependability and performance of products and systems. By employing various techniques and principles, reliability engineers contribute to the development of reliable and robust products that meet customer expectations and withstand the test of time.
The Intersection of Reliability Engineering and Modern Industries
In today's fast-paced and interconnected world, reliability engineering is particularly crucial in two key industries: manufacturing and tech. The application of reliability engineering principles in these industries has a profound impact on their operations and overall success.
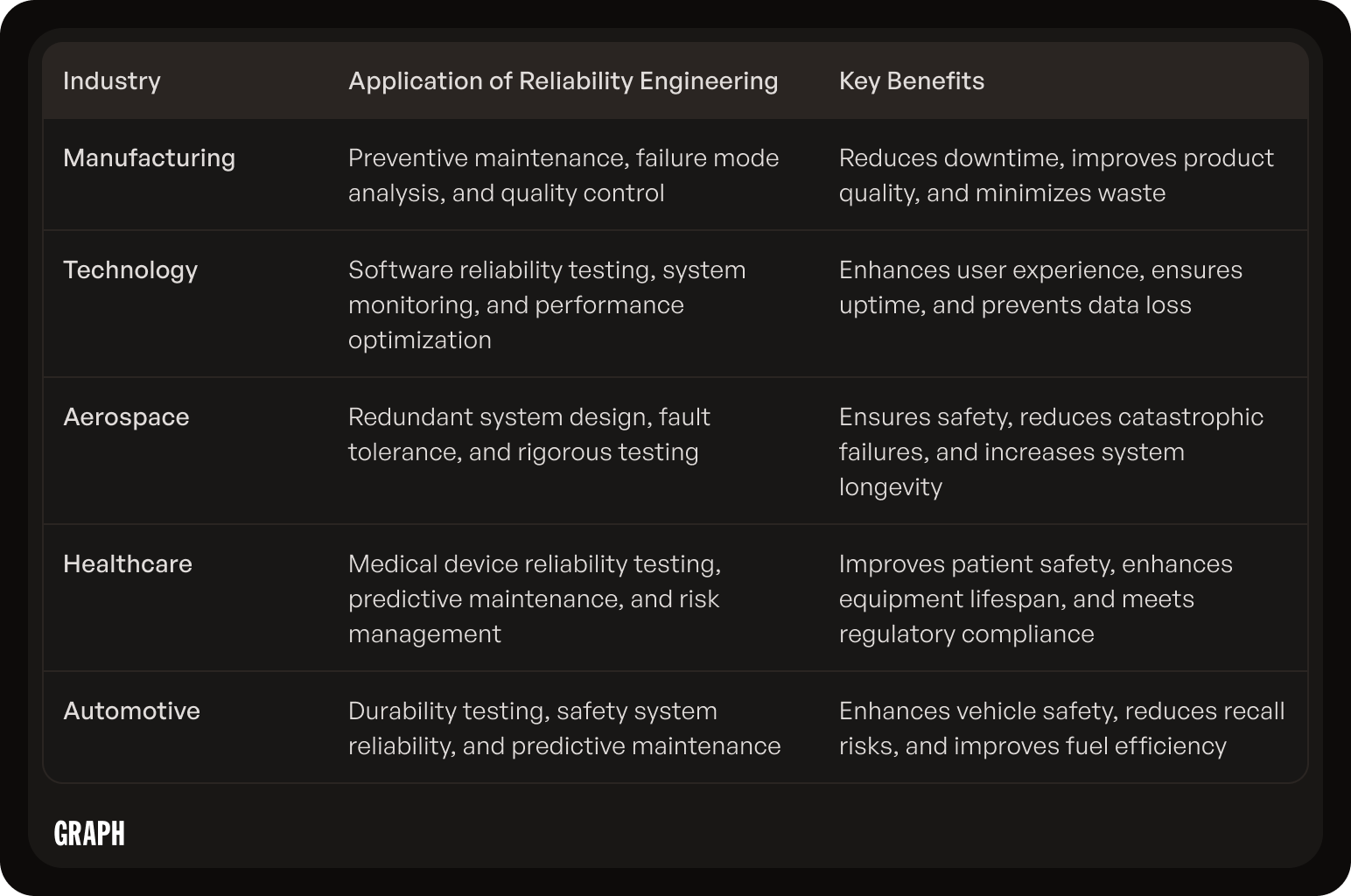
The Impact of Reliability Engineering on Manufacturing
In the manufacturing sector, where productivity, cost-efficiency, and product quality are of utmost importance, reliability engineering plays a fundamental role in ensuring smooth operations. By integrating reliability engineering principles into the design and production process, manufacturers can improve equipment uptime, reduce maintenance costs, and enhance overall product quality and consistency.
Reliability engineering also enables manufacturers to identify critical failure modes early in the product lifecycle, facilitating the implementation of preventive maintenance strategies to minimize downtime and optimize production. This proactive approach not only saves valuable time and resources but also ensures that products meet the highest standards of reliability and performance.
Furthermore, through data analysis and continuous improvement initiatives, reliability engineers can identify bottlenecks and inefficiencies in manufacturing processes, leading to increased productivity and reduced waste. By leveraging data-driven insights, manufacturers can make informed decisions to streamline operations, optimize resource allocation, and improve overall efficiency.
Reliability Engineering in the Tech Industry
The tech industry, characterized by rapid innovation and complex systems, heavily relies on reliability engineering to ensure seamless performance of software applications, websites, and digital platforms. Reliability engineering practices are essential in guaranteeing high availability, scalability, and responsiveness of digital services in the face of increasing user demands and ever-evolving technologies.
By conducting thorough reliability testing, tech companies can identify potential software bugs, performance bottlenecks, and system failures before they impact end-users. This proactive approach not only enhances the user experience but also safeguards the reputation and credibility of tech companies in an increasingly competitive market.
Reliability engineering also helps in capacity planning and in scaling infrastructure to handle peak loads, ensuring uninterrupted service delivery. By accurately predicting and preparing for spikes in user traffic, tech companies can avoid service disruptions, maintain customer satisfaction, and capitalize on business opportunities.
Furthermore, reliability engineering principles are instrumental in driving continuous improvement in software development processes. Through root cause analysis, data-driven decision-making, and the implementation of robust monitoring and alerting systems, reliability engineers enable tech companies to deliver reliable software and maintain customer satisfaction. This iterative approach fosters innovation, promotes efficiency, and ensures that software products meet the evolving needs and expectations of users.
The Benefits of Implementing Reliability Engineering
By embracing reliability engineering practices, companies across industries can unlock a range of benefits, resulting in enhanced product quality, reduced operational costs, and lower risks.
Enhancing Product Quality and Consistency
Reliability engineering enables businesses to identify and address potential product failures early on, resulting in improved product quality and reduced customer dissatisfaction. By systematically testing and analyzing products throughout their lifecycle, reliability engineers can identify design flaws, manufacturing defects, and other reliability issues, allowing companies to rectify them before they reach the market.
Moreover, by focusing on reliability, companies can ensure consistent product performance across different variations and batches, enhancing customer trust and loyalty.
Reducing Operational Costs and Risks
Reliability engineering practices lead to cost savings by minimizing downtime, reducing maintenance expenses, and optimizing resource utilization. By implementing preventive and predictive maintenance strategies based on reliability analysis, companies can avoid costly unplanned outages and system failures.
In addition, reliability engineering helps companies mitigate risks associated with product failures, safety incidents, and regulatory non-compliance. By proactively identifying and addressing potential risks, businesses can reduce the probability of expensive recalls, legal liabilities, and damage to their brand reputation.
Furthermore, implementing reliability engineering can also have a positive impact on the environment. By optimizing resource utilization and reducing waste, companies can contribute to sustainability efforts. For example, reliability engineers can identify opportunities for energy efficiency improvements, leading to reduced carbon emissions and a smaller ecological footprint.
Additionally, reliability engineering can drive innovation within organizations. By constantly monitoring and analyzing product performance, reliability engineers can identify areas for improvement and suggest innovative solutions. This continuous improvement mindset can foster a culture of innovation and creativity, leading to the development of new and improved products that meet the evolving needs of customers.
Challenges in Applying Reliability Engineering
Overcoming Resistance to Change
Implementing reliability engineering practices may face resistance from employees who are wary of change or hesitant to adopt new methodologies. This resistance can stem from various factors such as fear of the unknown, concerns about job security, or simply a lack of understanding about the benefits of reliability engineering. To overcome this challenge, organizations need to invest in comprehensive training programs that not only educate employees about the principles of reliability engineering but also address their concerns and provide reassurance.
Moreover, raising awareness about the tangible benefits of reliability engineering is crucial in gaining buy-in from employees at all levels of the organization. By showcasing real-world examples of how reliability engineering has improved product quality, reduced downtime, and enhanced customer satisfaction, organizations can effectively demonstrate the value of embracing reliability practices. Creating a culture of continuous improvement where feedback is encouraged, and successes are celebrated can further motivate employees to embrace change and actively participate in reliability initiatives.
Addressing the Skills Gap in Reliability Engineering
The rapid growth of technological advancements has resulted in a shortage of skilled reliability engineers in the industry. This skills gap poses a significant challenge for organizations looking to implement robust reliability engineering practices. To bridge this gap, organizations can take proactive measures such as investing in employee training programs that focus on developing specialized skills in reliability engineering.
Collaborating with educational institutions to design curriculum that aligns with industry needs and offering opportunities for hands-on experience through internships and apprenticeship programs can also help in nurturing the next generation of reliability engineers. Building a strong talent pipeline not only addresses the immediate skills shortage but also ensures the long-term sustainability of reliability engineering initiatives within the organization. By investing in the development of skilled professionals and creating pathways for continuous learning and growth, organizations can effectively navigate the challenges posed by the skills gap in reliability engineering.
The Future of Reliability Engineering
Emerging Trends in Reliability Engineering
In the era of Industry 4.0, reliability engineering is evolving to address the unique challenges posed by advanced technologies and interconnected systems. Some emerging trends include the integration of artificial intelligence (AI) and machine learning (ML) algorithms for predictive maintenance, the use of digital twins for virtual testing and optimization, and the application of data analytics to improve reliability prediction and decision-making.
One exciting aspect of the integration of AI and ML algorithms in reliability engineering is their ability to analyze vast amounts of data collected from sensors and other sources. These algorithms can detect patterns and anomalies that may indicate potential failures, allowing companies to take proactive measures to prevent them. By leveraging the power of AI and ML, reliability engineers can develop predictive maintenance strategies that optimize maintenance schedules, reduce costs, and minimize downtime.
Another emerging trend in reliability engineering is the use of digital twins. A digital twin is a virtual replica of a physical asset or system that allows engineers to simulate and test various scenarios without the need for physical prototypes. By creating a digital twin, reliability engineers can analyze the behavior of a system under different conditions, identify potential weaknesses, and optimize its performance. This virtual testing and optimization process not only saves time and resources but also enables engineers to make informed decisions that enhance reliability and efficiency.
Furthermore, reliability engineering is moving towards a more proactive and data-centric approach, where real-time monitoring, predictive analytics, and remote diagnostics enable companies to identify and mitigate potential failures before they occur. With advancements in IoT technology, sensors can collect real-time data on the health and performance of systems, providing valuable insights to reliability engineers. By analyzing this data using advanced analytics techniques, engineers can detect early warning signs of potential failures and take preventive actions, such as adjusting operating parameters or scheduling maintenance activities.
The Role of Reliability Engineering in Industry 4.0
In the context of Industry 4.0, reliability engineering plays a critical role in ensuring the smooth functioning of interconnected cyber-physical systems (CPS). By leveraging IoT sensors, big data analytics, and cloud computing, reliability engineers can monitor the health and performance of systems in real-time, enabling predictive maintenance, optimizing resource allocation, and reducing downtime.
Moreover, reliability engineering contributes to the wider adoption of smart manufacturing, where real-time data analysis and continuous improvement practices drive operational excellence and enable agile response to changing customer demands. By implementing reliability engineering principles and practices, companies can improve the reliability and performance of their manufacturing processes, leading to increased productivity, reduced costs, and enhanced customer satisfaction.
In conclusion, the future of reliability engineering is characterized by the integration of advanced technologies, such as AI, ML, digital twins, and data analytics. These emerging trends empower reliability engineers to proactively identify and mitigate potential failures, optimize system performance, and drive operational excellence in the era of Industry 4.0.
Conclusion
Reliability engineering has become a cornerstone in modern industries, offering numerous benefits to companies across sectors. By prioritizing reliability, businesses can enhance product quality, reduce costs and risks, improve customer satisfaction, and foster innovation and growth. As industries evolve and new technologies emerge, reliability engineering will continue to play a pivotal role in shaping the future of industrial excellence.