Defects vs Defectives: Understanding the Key Differences
In the world of manufacturing, the terms "defects" and "defectives" are often used interchangeably, leading to confusion and misunderstanding. However, it is crucial to differentiate between these two concepts in order to effectively address production issues and ensure optimal quality. In this article, we will explore the key differences between defects and defectives, their respective roles in production, misconceptions surrounding them, and why it is essential to navigate through these differences in the manufacturing industry.
Defining Defects and Defectives
The Concept of Defects
Defects refer to imperfections or deviations from desired specifications in a product or component. These can include flaws, blemishes, malformations, or irregularities that render the item unfit for its intended purpose. Defects can manifest at any stage of manufacturing, from raw material procurement to the final product assembly.
Identifying and rectifying defects promptly is essential, as they can adversely impact product quality, customer satisfaction, and brand reputation. Therefore, manufacturers must prioritize quality control measures to mitigate defects and ensure that products meet or exceed customer expectations.
Moreover, defects can be classified into various categories, such as design defects, manufacturing defects, and packaging defects. Design defects occur during the product's conception phase and can lead to functional issues or safety concerns. Manufacturing defects, on the other hand, arise during the production process and can result from equipment malfunctions, human error, or inadequate quality control. Lastly, packaging defects involve issues with how the product is packaged, which can affect its protection during shipping and storage.
The Concept of Defectives
In contrast, defectives are the individual products or components that possess defects and fail to meet the specified quality criteria. Defectives are the tangible manifestations of defects, and identifying and removing them from production is crucial to maintain a high level of product quality.
Defectives not only fail to meet quality requirements but can also result in wasted resources, increased production costs, and reduced efficiency. Proper management strategies and preventive measures are necessary to minimize the occurrence of defectives and optimize production processes.
The Role of Defects in Production
Impact of Defects on Quality
Defects have a direct impact on product quality. Even a single defect can compromise the functionality, aesthetics, or reliability of a product. When defects go unnoticed or disregarded, they can lead to customer complaints, returns, and ultimately tarnish the reputation of the manufacturer.
To maintain robust quality standards, manufacturers must implement rigorous inspection and testing procedures, ensuring that defects are identified and addressed before products reach the market. Regular quality audits and continuous improvement initiatives are also vital to identify underlying causes and prevent defects from recurring.
Moreover, the financial implications of defects cannot be understated. Beyond the cost of replacing or repairing defective products, there are hidden expenses associated with customer dissatisfaction, warranty claims, and potential legal issues. Therefore, investing in defect prevention is not only a matter of quality but also a strategic business decision.
Mitigating Defects in Production
Effective defect mitigation requires a multi-faceted approach, encompassing various processes and stakeholders. This includes thorough supplier evaluation, quality control at each production stage, and employee training to ensure awareness and adherence to quality standards.
Furthermore, fostering a culture of quality within the organization is essential for sustained defect reduction. By empowering employees to take ownership of quality and providing them with the necessary tools and training, manufacturers can create a proactive environment where defects are identified and resolved swiftly.
By adopting advanced manufacturing techniques, such as statistical process control and failure mode and effects analysis, manufacturers can proactively identify potential defect sources and implement preventive measures. Additionally, investing in reliable machinery, robust manufacturing processes, and effective defect tracking systems can help minimize defects and enhance overall product quality.
The Role of Defectives in Production
How Defectives Affect Production Efficiency
Defectives pose a significant challenge to production efficiency. When defective products are detected during or after production, it results in wasted time, materials, and labor. As a consequence, valuable resources are diverted away from productive operations, leading to decreased output and increased costs.
To mitigate the impact of defectives on production efficiency, manufacturers must establish effective scrap management systems, ensuring prompt identification, isolation, and disposal of defective products. Analyzing defect trends and root causes is also crucial to implement corrective actions and prevent recurrence, thereby enhancing overall production efficiency.
Strategies to Reduce Defectives
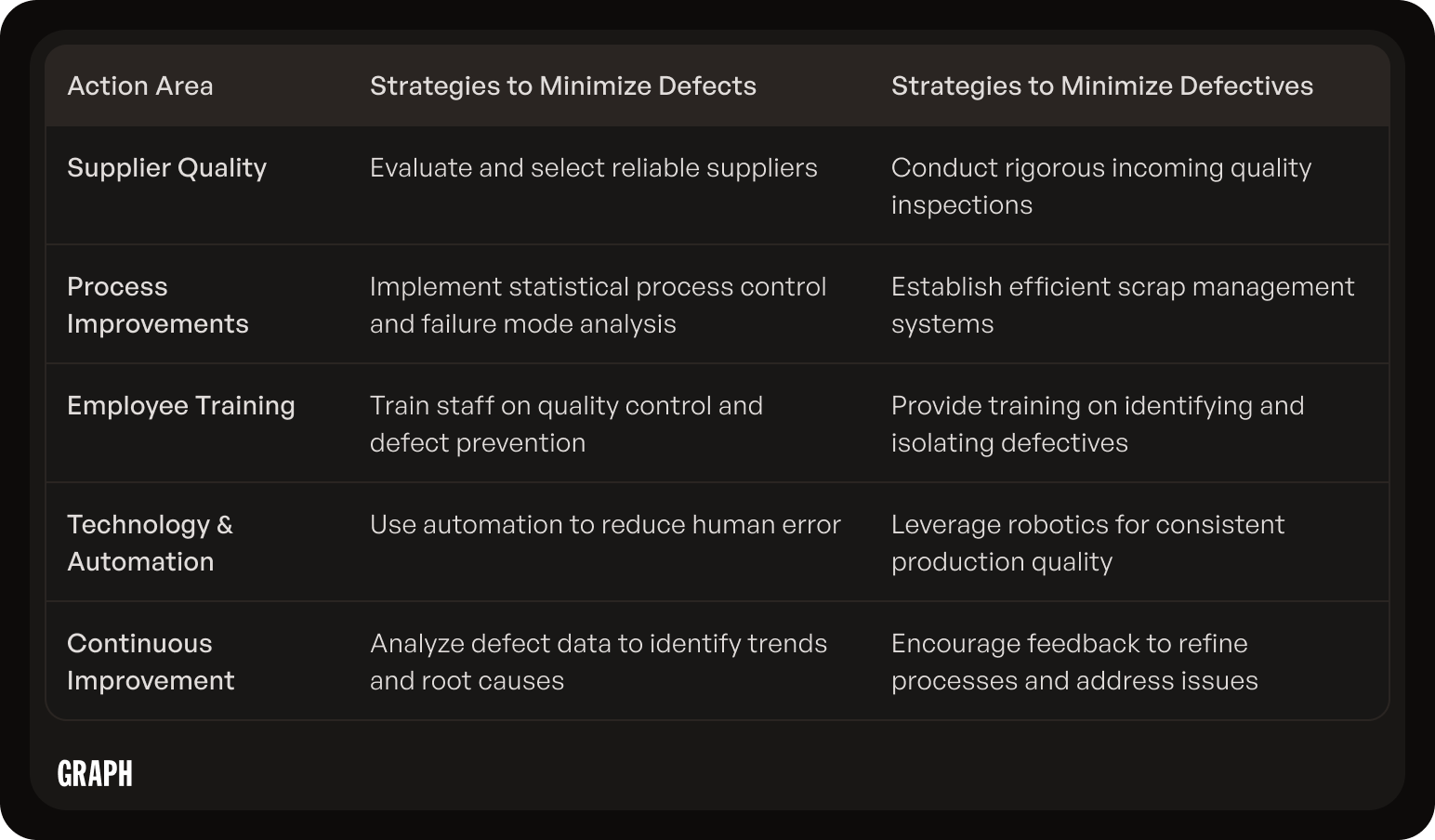
To curb defectives and optimize production efficiency, manufacturers must embrace a holistic approach. This includes fostering a culture of quality awareness and empowerment among employees, encouraging continuous improvement initiatives, and implementing quality control tools like statistical process control and process capability analysis.
Moreover, fostering strong relationships with suppliers, ensuring rigorous incoming quality inspection, and implementing real-time process monitoring can significantly reduce defectives. Embracing automation and robotics in production processes can also enhance precision, reducing the likelihood of defects and defectives.
One effective strategy to reduce defectives is to invest in employee training and development programs. By providing comprehensive training on quality control techniques and product specifications, manufacturers can empower their workforce to identify and address potential defects at an early stage. This not only improves production efficiency but also fosters a sense of ownership and pride among employees, leading to a higher level of commitment and dedication to producing high-quality products.
Furthermore, implementing a robust feedback system can play a crucial role in reducing defectives. By encouraging employees to report any observed defects or potential issues, manufacturers can quickly identify and rectify problems, preventing them from escalating into larger-scale production issues. This proactive approach not only saves valuable time and resources but also promotes a culture of continuous improvement and open communication within the organization.
Key Differences Between Defects and Defectives
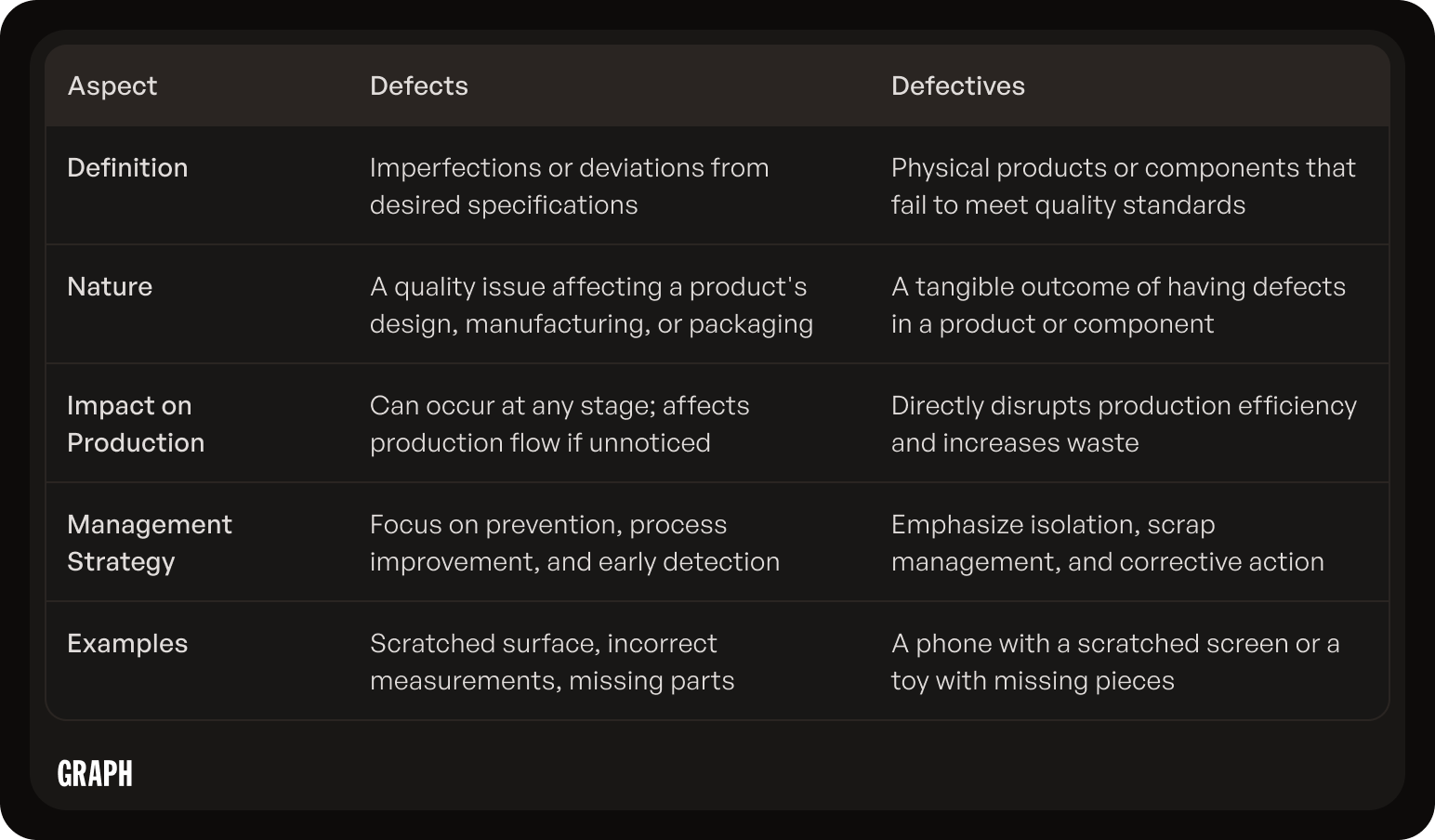
Comparing the Impact on Production
While defects and defectives are interconnected, they have distinct impacts on production processes. Defects can occur at any stage of manufacturing and require early detection and preventive measures. Defectives, on the other hand, represent the physical manifestation of those defects and directly affect production efficiency.
Defects, in their various forms, can arise during the design, manufacturing, or assembly stages. They can be caused by factors such as human error, equipment malfunction, or material defects. Detecting defects early is crucial to prevent them from propagating throughout the production process, leading to increased costs and delays. Implementing effective quality control measures, such as statistical process control and failure mode and effects analysis, can help identify and address defects before they impact the final product.
Defectives, on the other hand, are the tangible products that do not meet the required quality standards. They can range from minor imperfections to severe malfunctions, rendering the product unusable or unsafe. Defectives not only result in wasted resources but also disrupt the production flow, leading to decreased productivity and customer dissatisfaction. To optimize production efficiency, manufacturers must establish efficient scrap management systems that include proper disposal methods, recycling initiatives, and documentation of defective products for analysis and improvement.
Contrasting Management Strategies
The management strategies for defects and defectives differ based on their nature and impact. For defects, manufacturers must focus on process improvement, supplier quality management, and thorough inspection and testing procedures. The emphasis is on preventing defects from occurring and ensuring adherence to quality specifications.
Process improvement involves analyzing the root causes of defects and implementing corrective actions to eliminate or minimize their occurrence. This can include redesigning processes, enhancing training programs, and implementing error-proofing techniques. Additionally, effective supplier quality management is essential to ensure that raw materials and components meet the required standards, reducing the likelihood of defects in the final product. Thorough inspection and testing procedures, including quality audits and statistical sampling, help identify defects early and prevent their propagation.
On the other hand, managing defectives necessitates implementing effective scrap management systems, establishing robust incoming quality inspection, and fostering a culture of continuous improvement. The focus shifts toward minimizing the fallout from defectives, promptly identifying and isolating them, and taking corrective actions to prevent recurrence.
An efficient scrap management system involves proper segregation and disposal of defective products, ensuring that they do not find their way back into the production process. Establishing robust incoming quality inspection procedures helps identify potential defectives before they enter the production line, reducing the chances of producing faulty products. Furthermore, fostering a culture of continuous improvement encourages employees to actively participate in identifying and addressing the root causes of defectives, leading to long-term improvements in production efficiency and product quality.
Misconceptions About Defects and Defectives
Common Misunderstandings
Misconceptions surrounding defects and defectives are prevalent in the manufacturing industry. One common misunderstanding is regarding the interchangeability of these terms. While defects represent imperfections, defectives are the physical products that possess those defects.
It is important to note that defects can manifest in various forms, ranging from cosmetic blemishes to critical functional issues. Understanding the different types of defects is crucial for implementing effective quality control measures and ensuring customer satisfaction.
Another misconception is the belief that defects are solely the responsibility of the manufacturing department. In reality, defects can arise from various sources, such as design flaws, incorrect materials, or inadequate process controls. Addressing defects requires a collaborative effort among multiple stakeholders, including engineering, quality control, and supply chain management.
Clarifying the Confusion
Clear communication and understanding are vital to address these misconceptions. By educating employees and stakeholders about the distinctions between defects and defectives, manufacturers can foster a deeper understanding of quality management and their respective responsibilities.
Incorporating comprehensive training programs, providing visual aids and examples, and encouraging open discussions can help dissipate confusion and ensure a unified approach towards addressing defects and defectives.
Furthermore, implementing robust quality assurance processes and conducting regular audits can help identify potential sources of defects early in the production cycle, preventing costly rework and customer dissatisfaction. By proactively addressing quality issues, manufacturers can enhance their reputation and competitiveness in the market.
The Importance of Differentiating Between Defects and Defectives
Implications for Quality Control
Differentiating between defects and defectives empowers manufacturers to implement more targeted quality control measures. By focusing on early detection, prevention, and continuous improvement initiatives, manufacturers can minimize defects and enhance overall product quality.
Moreover, understanding the impact of defects on defectives allows manufacturers to identify root causes, implement corrective actions, and optimize quality control processes. Effective defect tracking and analysis also play a crucial role in ensuring consistent product quality and customer satisfaction.
Delving deeper into this differentiation, it is essential to recognize that defects refer to any deviation from the specified product requirements, while defectives are products that contain defects. This distinction is pivotal in quality control as it enables manufacturers to pinpoint specific areas in the production process that require attention.
Implications for Production Efficiency
The differentiation between defects and defectives is equally vital for maintaining efficient production processes. By addressing defects at their source and implementing preventive measures, manufacturers can reduce the occurrence of defectives and optimize production efficiency.
Efficient scrap management, real-time process monitoring, and robust corrective actions help minimize the impact of defectives on production efficiency. Embracing technology, automation, and continuous improvement initiatives further streamline operations, reducing both defects and defectives.
Furthermore, integrating defect and defective data into overall production analytics provides valuable insights for process optimization and resource allocation. By leveraging this information, manufacturers can make informed decisions to enhance productivity, minimize waste, and drive continuous improvement across all facets of production.
Conclusion: Navigating Defects and Defectives in Production
In conclusion, while defects and defectives are often used interchangeably, they are distinct concepts that require different approaches in manufacturing. Understanding the differences between defects and defectives is critical for developing effective quality control and production strategies.
By prioritizing early detection, prevention, and continuous improvement, manufacturers can minimize defects and enhance product quality. Efficient management of defectives through proper scrap management, incoming quality inspection, and corrective actions optimizes production efficiency and reduces waste.
Clear communication, education, and a collaborative approach help to dispel misconceptions surrounding defects and defectives. Prioritizing differentiation between these concepts and implementing appropriate management strategies enable manufacturers to achieve superior product quality, optimize production efficiency, and satisfy customer expectations in the competitive manufacturing industry.